As temperatures rise and spring transitions into summer, industrial environments become more challenging for cooling systems. At TEYU S&A, we recommend targeted seasonal maintenance to ensure your
1. Maintain Adequate Clearance for Efficient Heat Dissipation
Proper clearance around the chiller is critical to maintaining effective airflow and preventing heat buildup. The requirements vary based on the industrial chiller’s power:
❆ Low-power chiller models: Ensure at least 1.5 meters of clearance above the top air outlet and 1 meter around the side air inlets.
❆ High-power chiller models: Provide at least 3.5 meters of clearance above and 1 meter at the sides to prevent hot air recirculation and performance degradation.
Always install the unit on a level surface with no obstruction to airflow. Avoid tight corners or confined spaces that restrict ventilation.
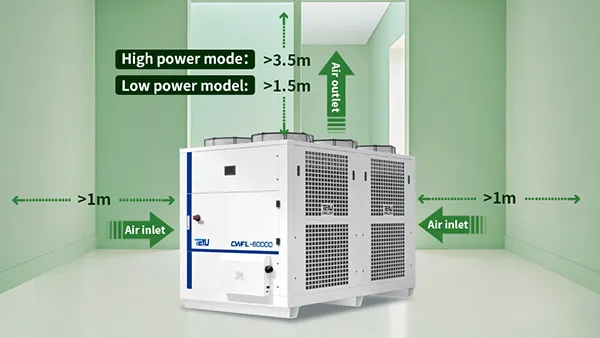
2. Avoid Installing in Harsh Environments
Avoid Chillers should be kept away from areas with the following risks:
❆ Corrosive or flammable gases
❆ Heavy dust, oil mist, or conductive particles
❆ High humidity or extreme temperatures
❆ Strong magnetic fields
❆ Direct exposure to sunlight
These factors may severely affect performance or shorten the equipment's lifespan. Choose a stable environment that meets the chiller's ambient temperature and humidity requirements.
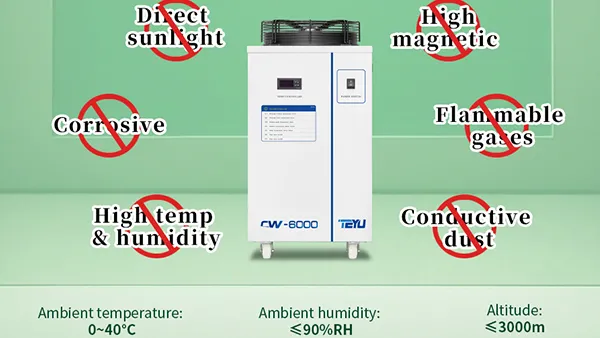
3. Smart Placement: What to Do & What to Avoid
❆ Do place the chiller:
On flat, stable ground
In well-ventilated areas with sufficient space around all sides
❆ Don't:
Suspend the chiller without support
Place it near heat-generating equipment
Install in unventilated attics, narrow rooms, or under direct sunlight
Proper positioning reduces thermal load, enhances cooling performance, and supports long-term reliability.
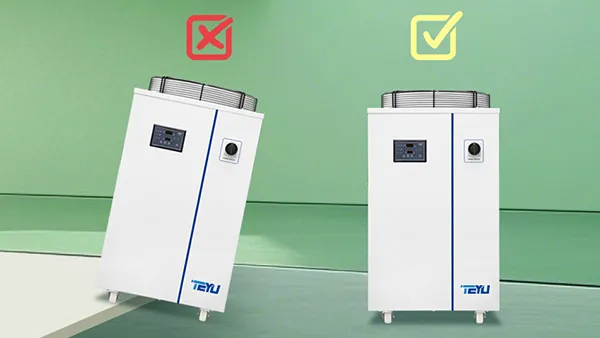
3. Keep Air Filters & Condensers Clean
Spring often brings increased airborne particles such as dust and plant fibers. These can accumulate on filters and condenser fins, obstructing airflow and reducing cooling efficiency.
Clean Daily in Dusty Conditions: We recommend daily cleaning of the air filter and condenser during dusty seasons.
⚠ Use Caution: When cleaning with an air gun, keep the nozzle about 15 cm from the fins and blow perpendicularly to avoid damage.
Routine cleaning helps prevent over-temperature alarms and unplanned downtime, ensuring stable cooling throughout the season.
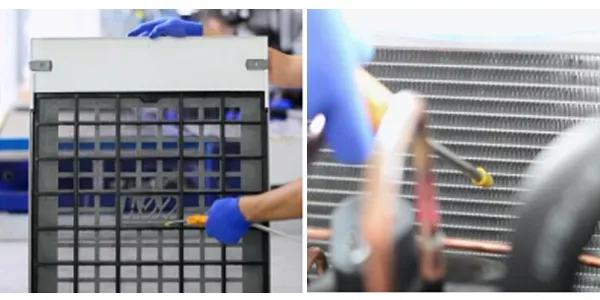
Why Spring & Summer Maintenance Matters
A well-maintained TEYU water chiller not only ensures consistent cooling but also helps prevent unnecessary wear and energy loss. With smart placement, dust control, and environmental awareness, your equipment stays in optimal condition, supporting continuous productivity and extending service life.
Spring & Summer Reminder:
During spring and summer maintenance, prioritize tasks such as ensuring adequate ventilation, regularly cleaning air filters and condenser fins, monitoring ambient temperature, and checking water quality. These proactive steps help maintain stable chiller performance under warmer conditions. For additional support or technical guidance, feel free to contact our dedicated service team at service@teyuchiller.com.
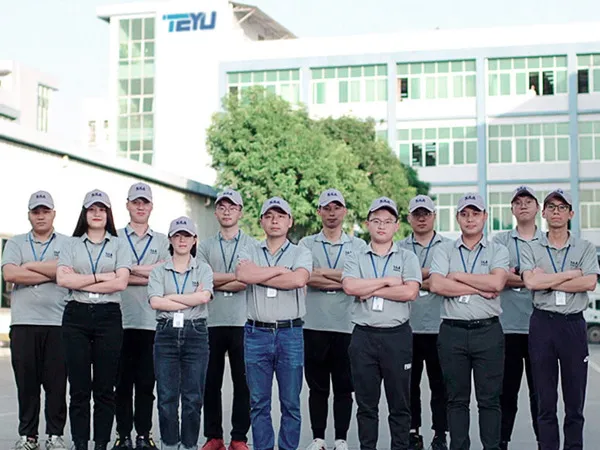
Source: https://www.teyuchiller.com/spring-and-summer-maintenance-guide-for-teyu-water-chillers.html